粒子は自然に存在しているものもありますが、目的に合わせて必要な大きさに作りこむことで、工業的に機能を高めることができます。
ここでは、粒子の大きさを目的通りにしていくためにとられる手法を見てみます。
粒子を作る方法には、もともと大きいものを小さくしていくやり方と、もともと小さいものを大きくしていくやり方があります。
大きい原材料から粒子を作る方法
粉砕
工業用のミルなどを使って、原材料を細かく砕き粒子にしていきます。コーヒー豆を挽くのと同じことですが、材料の成分や目的によって、挽き方を変えていきます。
例
セメント材料、食品、医薬品、塗料など
設備が必要
かならず必要なのは粉砕機です。
刃の大きさや形、角度は材料や目的とする粒子径や、原料の高度などによって変わりますが、コーヒーミルや胡椒のミルのように1軸の回転する刃が筒の中にある粒子をつぶしていくタイプのものや、シュレッダーのように2軸の回転する刃が、軸の間をすり抜ける際に粒子をつぶしていくタイプのものがあります。
ただし大きい塊から一気に微粉を作るのか、刃に負荷がかかったり、工程に時間がかかったりするため数10㎝あるような塊は、先に数センチにくだき、工程を何段階かに分けて徐々に小さく砕いていきます。
また、粉砕工程では摩擦によって熱が発生するので、その熱で粒子や設備そのものがダメージを受けるようであれば、その対策、例えば冷却設備などが追加で必要です。
均一な粒子を作るのは意外に難しい
ポケットの中のビスケット、叩いても真っ二つにはならないですよね?
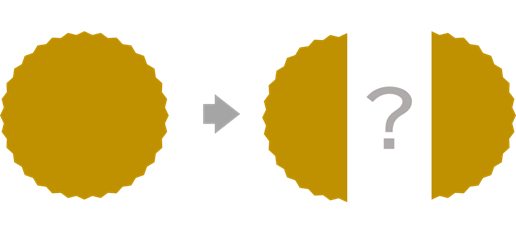
たいていは下のようにバキバキに割れます。 しかも割れ方は毎回変わります。
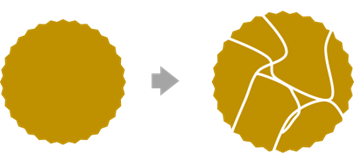
実際にいろんな大きさの粒子ができてしまったら、篩ったり遠心分離したりしながら、目的外の大きさになってしまった粒子をそぎ落としていく作業を行います。
微粉が出る
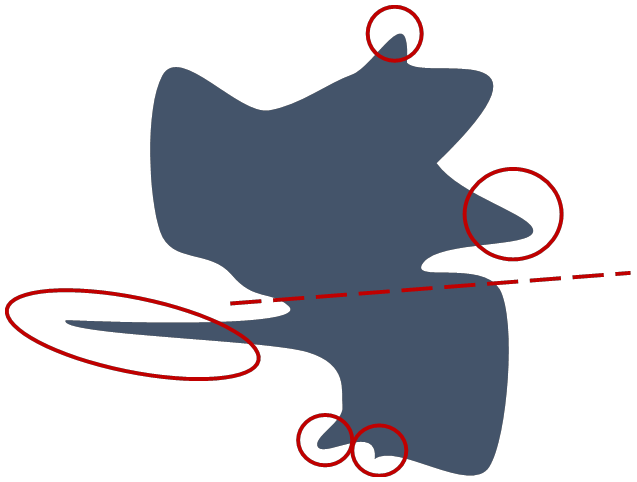
粒子を目的の大きさにそぎ落としていくと、どうしてもミルの歯や粒子どうしの接触などで粒子の脆いところがから砕け、徐々に粒子は小さくなります。 脆いところとは、粒子表面のとがったところ○や括れたところ…などで、この○が砕けるとメインの粒子の粒子径はさほど変化がなく、しかしたくさんの微細な粒子(=微粉)が発生します。
小さい原材料から粒子を作る方法
重合・合成
例
トナー粒子、吸水性ポリマー、シリカゲルなど
比較的粒子が均質になる
分子レベルから合成していくため、同時に作られたものの粒子径は比較的近くなり、粒子の形も揃うことが多くなります。
造粒
例
医薬品、食品
方法
スプレー造粒:造粒機内でスラリー(=粒子の入った液滴)を噴射し、瞬時に水分を飛ばすことで丸く、大きさのそろった粒子を作ることができます。
湿式造粒:粉体に結着剤などを入れて、混合して作りこみます。
乾式造粒:粉体をそのまま圧縮したものを再度粉砕する。
扱いやすさが改善する
造粒して粒子径が大きくなり、ゴツゴツしていた粒子の形が丸くなると、粒子が転がりやすく(=流動性が改善)なり、配管や容器をきれいに流れるようになります。
粒子の流れやすさが改善すると、複数の粒子を混合するときに均等に混ざりあうようになるので、最終形態の品質が均一になります。 薬局で買う胃薬を想像してもらえればわかりやすいかもしれません。 1回服用するごとに、入っている成分にばらつきがあると困りますよね? きれいに混ざり合うよう、きちんと管理されています。
そのほか粉体の飛散の抑止目的でも造粒が行われることがあります。
それぞれの方法には可能なサイズ帯がある
ここまで粒子を作るための3つの方法を紹介しましたが、これらはそれぞれ得意とする領域があります。
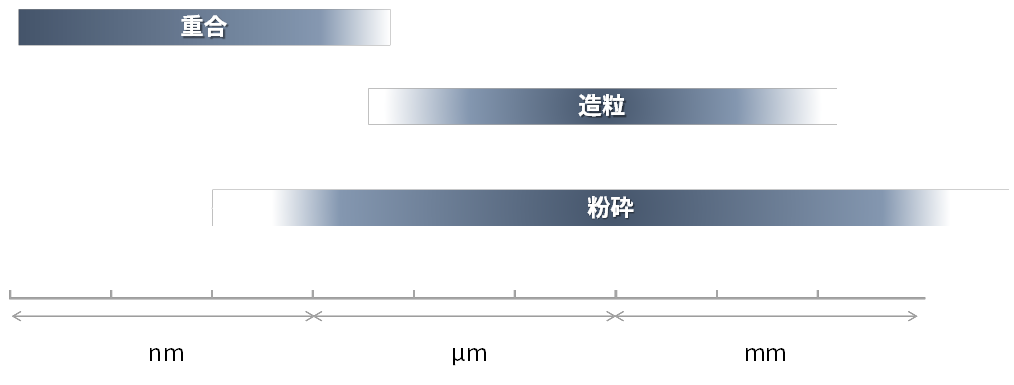
重合は分子の領域でもあるナノサイズ~数ミクロン、造粒はサブミクロン~数ミリを得意とします。
粉砕は一見するとカバーする領域が広くなっていますが、サブミクロン以下の粉砕を行おうとすると、粉砕に必要な時間が長くなったり、粉砕した粒子が凝集塊を作ったりするので、現状のサイズに合わせて粉砕機を組み合わせて、徐々に小さくしていきます。
特に、数10mm(=数センチ)以上の大きな岩状のものになると始めはある程度まで小さくする手法が必須になりますが、これを破砕と言います。